Iron & Steel Ship Construction (1/2)
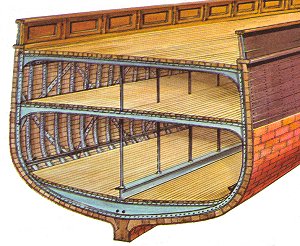
Iron and steel began to replace wood in ship construction in the middle to late 1800s. Timber-poor Europe ( especially England ) led in the development of iron ships, while America, with its vast reserves of lumber, continued to build wooden ships for some time longer. However, as the economical size of ships grew to surpass what could be built of wood, America too began constructing iron ships. For a few years, composite ships were built with iron frames and wooden skins, as seen at right, but difficulties with corrosion between the wood and metal soon led to hulls built completely of metal, both sailing ships and steamers.
Design
Ship design is a mass of compromises. There is a balance to be struck between the speed that is desired for the ship to make the fastest possible passage, and the fuel consumption, because getting this balance wrong at a time when oil prices are rising can make a ship rapidly uneconomic. There are the dimensions of the ship - length, breadth, depth, and most important draught - to be considered, because there is no point designing a ship that will be too big or too deep to get into the ports she is scheduled to visit. The type of cargo will dictate the design of the increasingly specialist ships of today - some vessels are so specialized that they can carry but one commodity. Naval architects design a ship according to the needs of the ship-owner, who will supply certain broad criteria, such as the cargo requirements, the speed and fuel consumption, along with the dimensional "envelope" and any special operating conditions such as the requirement to run in ice, or pass under low bridges.
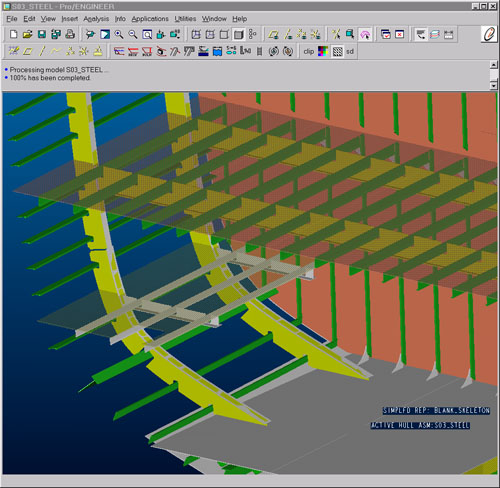
Unlike new designs of cars, or airplanes, there is no such thing as a prototype to assist a naval architect in refining his design: he has to get it right the first time. However, the modern naval architect is assisted by powerful computers, and may also use test tanks to try out models of the vessel, to check its sea keeping characteristics and performance in different weather conditions, before the shipbuilder starts to cut steel to build the ship as designed.
There is a great deal at stake, and naval architecture is a precise science, although experience of what has been designed and built before plays an important part. The ship has to float, but at exactly the draught that has been specified. Stability is critical, both from the point of the ability of the ship to behave acceptably in rough seas and so that the loading of cargo makes her neither top nor bottom heavy. The underwater shape of the hull is a critical factor in the performance of the ship, in the resistance the hull offers to the passing water, which will greatly affect the power requirements and fuel consumption to meet the desired speed. The designer is looking to optimize the hull shape so that the compromises which have been made between the various criteria result in the best possible solution and the most efficient hull design.
Because a ship has to operate in a hostile environment, much of the naval architect's work will be devoted to ensuring that the ship is strong enough for a long, hard life of 25 years and upwards in a corrosive, salt-encrusted atmosphere. There is no room for error and the designer has rules provided for him by the classification societies which prescribe strengths and thicknesses of the structure, which has to cope both with the stresses of shifting weights as cargo is loaded and discharged, or tanks pumped out, and the dynamic and often violent effects of the sea. A ship may be made of steel, but it must be assembled in such a way that there is built-in elasticity to cope with the huge forces of the sea that will flex the whole ship, subject it to huge weights and pressures, and threaten, if it were not well designed, to tear the ship apart.
Construction
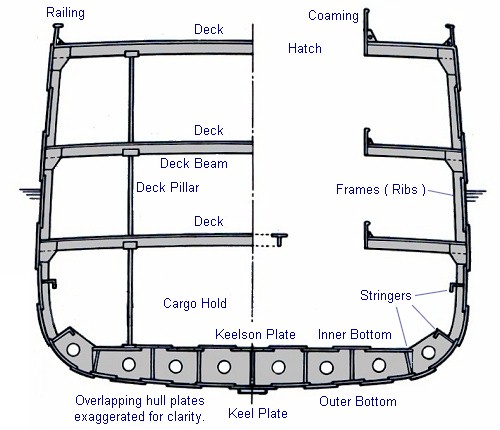
An iron ( or steel ) ship is constructed similarly to a wooden ship. First, a keel plate is laid, then the stem and sternpost are erected. U-shaped "frames", the equivalent of ribs in a wooden ship, are constructed and attached to the keel plate. The frames are capped along the centerline with a keelson plate for additional strength, and longitudinal stringers are installed between the ribs. Finally, inner and outer hull plating is attached, decks are constructed inside, and machinery and other finishing features are installed.
The uppermost level that runs the full length of the hull is called the main deck. Below that are various lower decks, depending on the size of the vessel. The superstructure is built up above the main deck, and its levels are also referred to as decks, although this is technically incorrect. The breezy uppermost level of the superstructure is called the hurricane deck, and below it are variously the boat deck, cabin deck, promenade deck, and others, depending on the size of the vessel and the creativity of the people that make up names for decks.
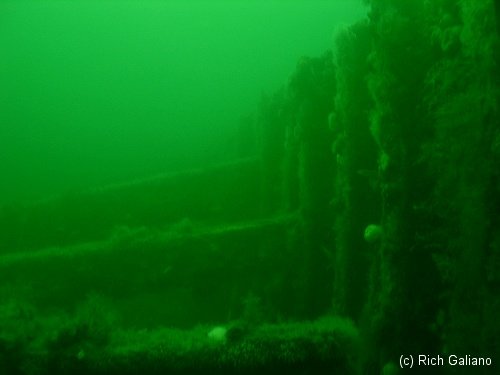
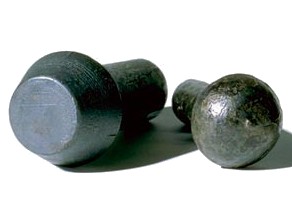
On old vessels, frames, keel, hull plates, and all other major components were attached using overlapping construction and rivets ( right ) or bolts. Rivets were superior since they provided a near-watertight joint with no special sealing. Prior to World War II, welded ship construction was considered to be experimental, but during the war, the technology was developed to a much greater degree and replaced riveting entirely. However, most of the shipwrecks a diver will encounter predate the war in construction, and will therefore be of the older riveted construction. Notable exceptions include the Pinta and the Stolt Dagali.
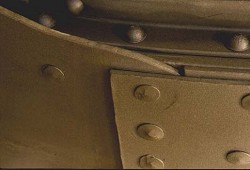
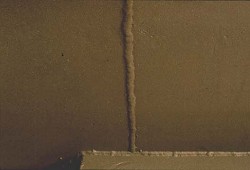
Riveted ( left ) and welded ( right ) joints
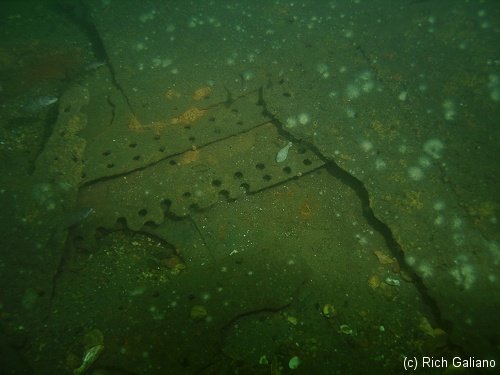
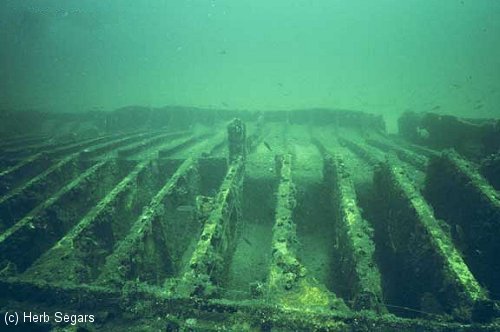
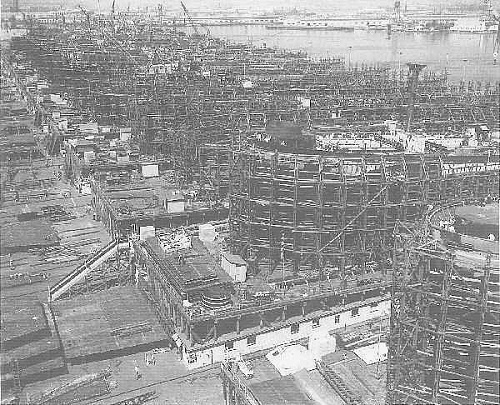
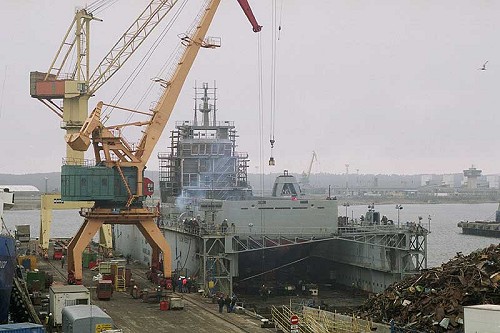
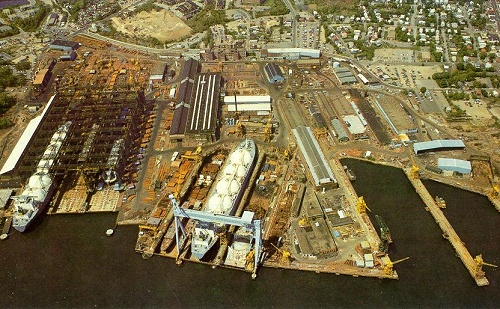
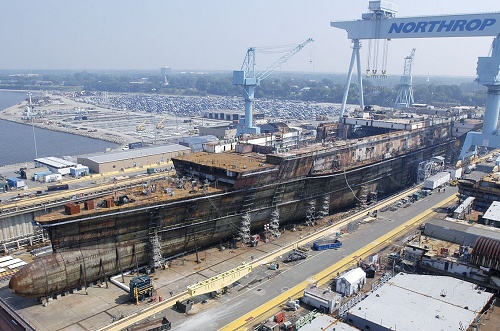
YO-65 class tankers in various stages of construction and fitting-out during World War II. Many examples of this class of small tanker are found along the coast as artificial reefs.
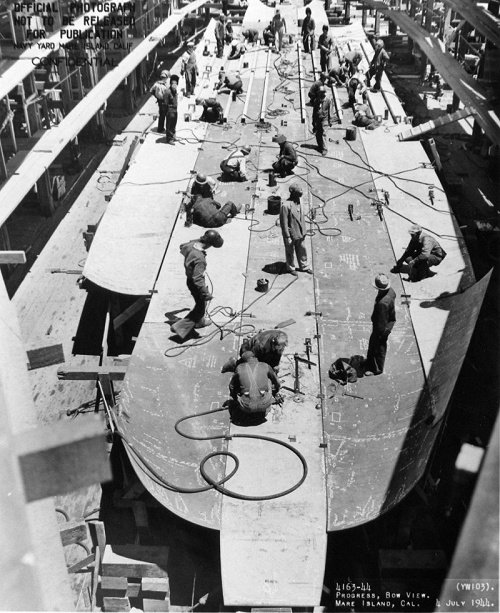

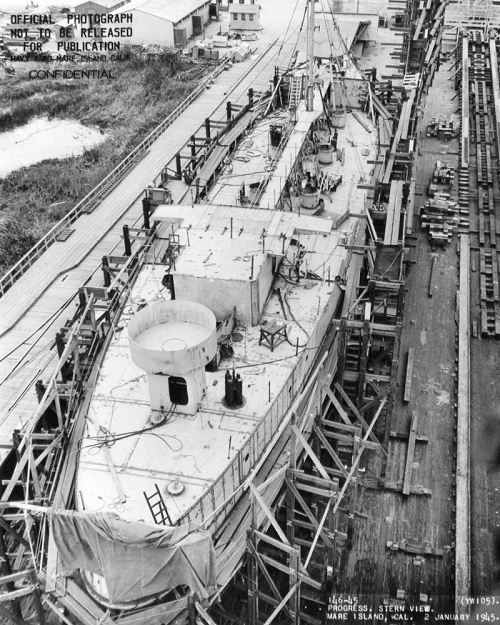
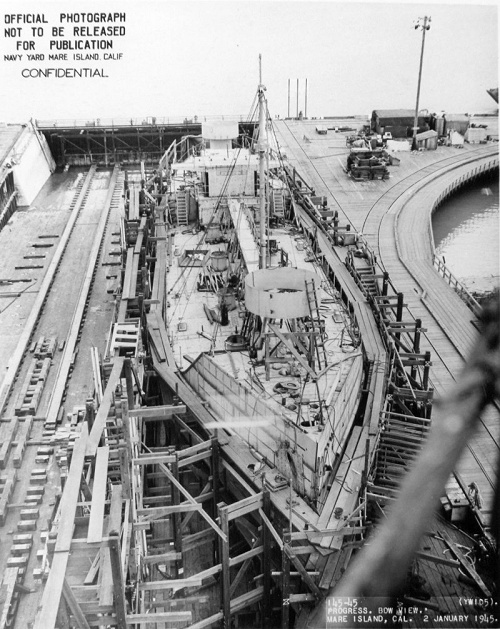
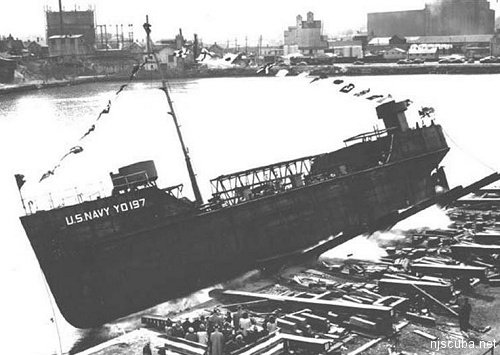
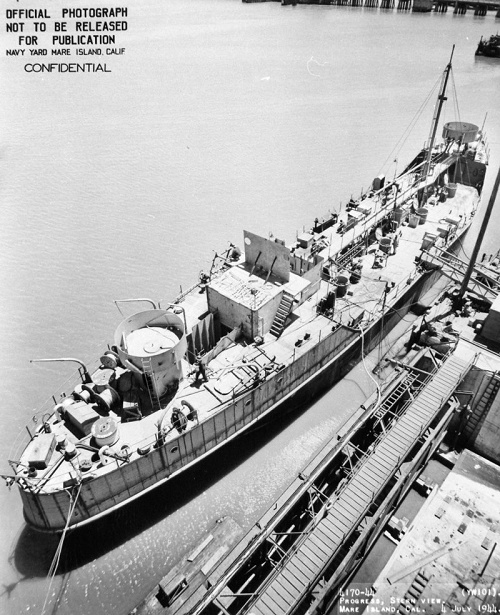
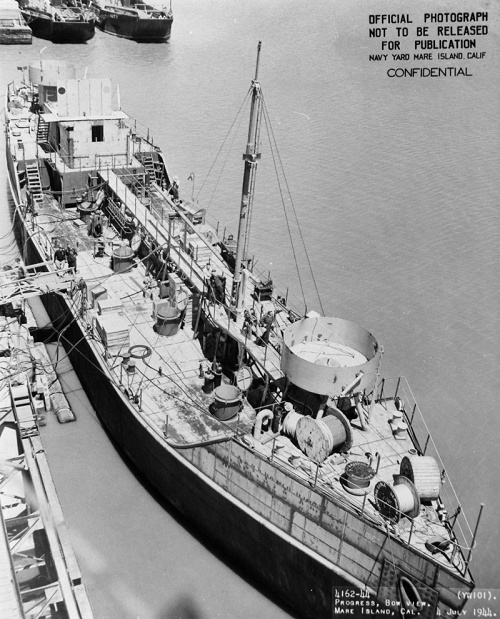
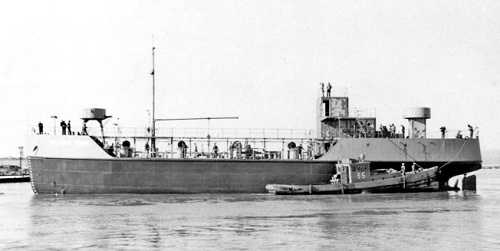
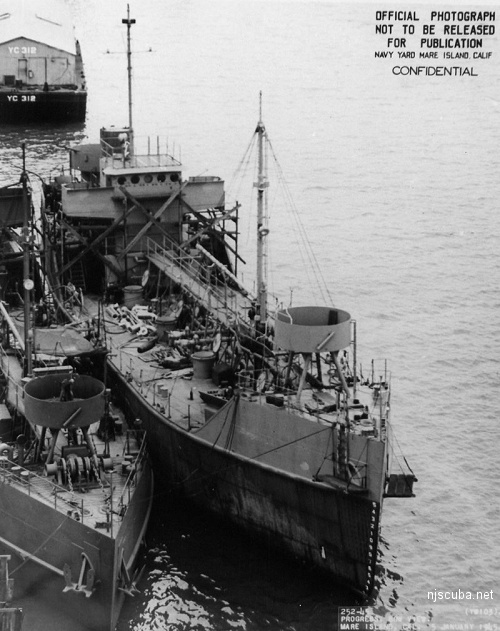
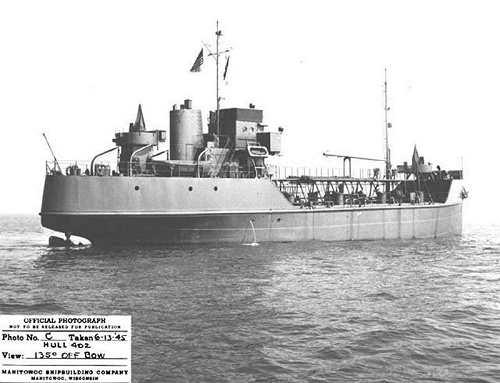