Polymer Materials (1/3)
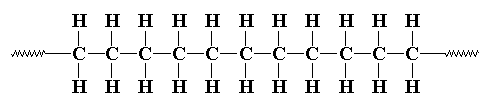
Polymer materials - rubbers, plastics, and silicones - are not really of interest as artifacts. They are, however, among the most important materials to divers: without neoprene, nylon, and a bewildering range of other polymer materials, we would not have most of the equipment that makes diving possible!
A polymer is a chemical compound with a high molecular weight consisting of a number of structural units linked together by covalent bonds. The simple molecules that may become structural units are themselves called monomers; two monomers combine to form a dimer, and three monomers, a trimer. A structural unit is a group having two or more bonding sites. A bonding site may be created by the loss of an atom or group, such as H or OH, or by the breaking up of a double or triple bond, as when ethylene, H2C=CH2, is converted into a structural unit for polyethylene, -H2C-CH2- .
Incidentally, stick a hydrogen "H" onto each end of this illustration in place of the squiggly lines, and you have C11H24 - a fairly common form of gasoline! Many artificial polymers are synthesized from fuel oils; there is no clear delineation between the two. Likewise, many polymers combust just as readily as fuel oils, although often with toxic products, especially those containing chlorine.
In a linear polymer, the structural units are connected in a chain arrangement and thus need only be bifunctional, i.e., have two bonding sites. When the structural unit is trifunctional ( has three bonding sites, ) a nonlinear, or branched, polymer results. Ethylene, styrene, and ethylene glycol are examples of bifunctional monomers, while glycerin and divinyl benzene are both polyfunctional. Polymers containing a single repeating unit, such as polyethylene, are called homopolymers. Polymers containing two or more different structural units, such as phenol-formaldehyde, are called copolymers.
All polymers can be classified as either addition polymers or condensation polymers. An addition polymer is one in which the molecular formula of the repeating structural unit is identical to that of the monomer, e.g., polyethylene and polystyrene. A condensation polymer is one in which the repeating structural unit contains fewer atoms than that of the monomer or monomers because of the splitting off of water or some other substance, e.g., polyesters and polycarbonates.
Many polymers occur in nature, such as silk, cellulose, natural rubber, and proteins. In addition, a large number of polymers have been synthesized in the laboratory, leading to such commercially important products as plastics, synthetic fibers, and synthetic rubber. Polymerization, the chemical process of forming polymers from their component monomers, is often a complex process that may be initiated or sustained by heat, pressure, or the presence of one or more catalysts.
Rubber
Rubber is any solid substance that upon vulcanization becomes elastic; the term includes natural rubber ( caoutchouc ) and synthetic rubber. The term elastomer is sometimes used to designate synthetic rubber only and is sometimes extended to include caoutchouc as well.
Chemistry and Properties

All rubber-like materials are polymers, which are high molecular weight compounds consisting of long chains of one or more types of molecules, such as monomers. Vulcanization ( or curing ) produces chemical links between the loosely coiled polymeric chains; elasticity occurs because the chains can be stretched and the crosslinks cause them to spring back when the stress is released. Natural rubber is a polyterpene, i.e., it consists of isoprene molecules linked into loosely twisted chains. The monomer units along the backbone of the carbon chains are in a cis arrangement and it is this spatial configuration that gives rubber its highly elastic character. In gutta-percha, which is another natural polyterpene, the isoprene molecules are bonded in a trans configuration leading to a crystalline solid at room temperature. Unvulcanized rubber is soluble in a number of hydrocarbons, including benzene, toluene, gasoline, and lubricating oils.
Rubber is water repellent and resistant to alkalies and weak acids. Rubber's elasticity, toughness, impermeability, adhesiveness, and electrical resistance make it useful as an adhesive, a coating composition, a fiber, a molding compound, and an electrical insulator. In general, synthetic rubber has the following advantages over natural rubber: better aging and weathering, more resistance to oil, solvents, oxygen, ozone, and certain chemicals, and resilience over a wider temperature range. The advantages of natural rubber are less buildup of heat from flexing and greater resistance to tearing when hot.

Vulcanization is the treatment of rubber to give it certain qualities, e.g., strength, elasticity, and resistance to solvents, and to render it impervious to moderate heat and cold. Chemically, the process involves the formation of cross-linkages between the polymer chains of the rubber molecules. Vulcanization is accomplished usually by a process invented by Charles Goodyear in 1839, involving combination with sulfur and heating. A method of cold vulcanization ( treating rubber with a bath or vapors of a sulfur compound ) was developed by Alexander Parkes in 1846.
Rubber for almost all ordinary purposes is vulcanized; exceptions are rubber cement, crepe-rubber soles, and adhesive tape. Hard rubber is vulcanized rubber in which 30% to 50% of sulfur has been mixed before heating; soft rubber contains usually less than 5% of sulfur. After the sulfur and rubber ( and usually an organic accelerator, e.g., an aniline compound, to shorten the time or lower the heat necessary for vulcanization ) are mixed, the compound is usually placed in molds and subjected to heat and pressure. The heat may be applied directly by steam, by steam-heated molds, by hot air, or by hot water. Vulcanization can also be accomplished with certain peroxides, gamma radiation, and several other organic compounds.
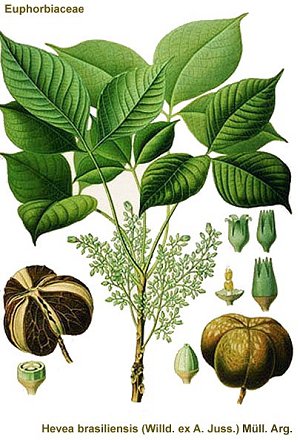
The finished product is not sticky like raw rubber, does not harden with cold or soften much except with great heat, is elastic, springing back into shape when deformed instead of remaining deformed as unvulcanized rubber does, is highly resistant to abrasion and to gasoline and most chemicals, and is a good insulator against electricity and heat. Many synthetic rubbers undergo processes of vulcanization, some of which are similar to those applied to natural rubber. The invention of vulcanization made possible the wide use of rubber and aided the development of such industries as the automobile industry.
Natural Rubber
Natural rubber is obtained from the milky secretion ( latex ) of various plants, but the only important commercial source of natural rubber ( sometimes called Para rubber ) is the tree Hevea brasiliensis. The only other plant under cultivation as a commercial rubber source is guayule ( Parthenium argentatum ) a shrub native to the arid regions of Mexico and the SW United States. The easiest way to see raw latex for yourself is to pick a Dandelion. The sticky white liquid that drips from the broken stem is latex.
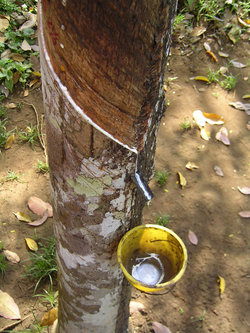
To soften the rubber so that compounding ingredients can be added, the long polymer chains must be partially broken by mastication, mechanical shearing forces applied by passing the rubber between rollers or rotating blades. Thus, for most purposes, the rubber is ground, dissolved in a suitable solvent, and compounded with other ingredients, e.g., fillers and pigments such as carbon black for strength and whiting for stiffening; antioxidants; plasticizers, usually in the form of oils, waxes, or tars; accelerators; and vulcanizing agents. The compounded rubber is sheeted, extruded in special shapes, applied as a coating or molded, then vulcanized. Most Para rubber is exported as crude rubber and prepared for market by rolling slabs of latex coagulated with acid into thin sheets of crepe rubber or into heavier, firmly pressed sheets that are usually ribbed and smoked.
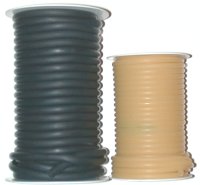
An increasing quantity of latex, treated with alkali to prevent coagulation, is shipped for processing in manufacturing centers. Much of it is used to make foam rubber by beating air into it before pouring it into a vulcanizing mold. Other products are made by dipping a mold into latex ( e.g., rubber gloves ) or by casting latex. Sponge rubber is prepared by adding to ordinary rubber a powder that forms a gas during vulcanization.
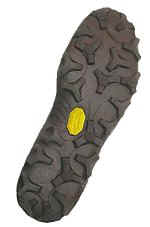
Most of the rubber imported into the United States is used in tires and tire products; other items that account for large quantities are belting, hoses, surgical tubing, insulators, valves, and gaskets. Vibram is a trade name for both a rubber formulation and a tread design used extensively in footwear, dating back to the 1930s. Uncoagulated latex, compounded with colloidal emulsions and dispersions, is extruded as thread, coated on other materials, or beaten to a foam and used as sponge rubber. Used and waste rubber may be reclaimed by grinding followed by devulcanization with steam and chemicals, refining, and remanufacture.
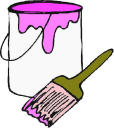
Most white glues, such as Elmer's, are latex-based. The solvent in Elmer's all-purpose school glue is water. When the water evaporates, the polyvinylacetate (PVA) latex that has spread into a material's pores and crevices forms a flexible bond. Another use for latex that is often overlooked is in paint. Most modern water-based paints ( as well as driveway sealers, etc ) use synthetic latex for a binding agent, which acts much as it does in glue. So chances are, your walls are coated with rubber!
Synthetic Rubber

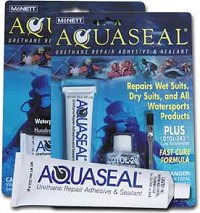
The more than one dozen major classes of synthetic rubber are made of raw material derived from petroleum, coal, oil, natural gas, and acetylene. Many of them are copolymers, i.e., polymers consisting of more than one monomer. By changing the composition it is possible to achieve specific properties desired for special applications. The earliest synthetic rubbers were the styrene-butadiene copolymers, Buna S, and SBR, whose properties are closest to those of natural rubber. SBR is the most commonly used elastomer because of its low cost and good properties; it is used mainly for tires. Other general-purpose elastomers are cis-polybutadiene and cis-polyisoprene, whose properties are also close to that of natural rubber.
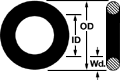
Among the specialty elastomers are copolymers of acrylonitrile and butadiene that were originally called Buna N and are now known as nitrile elastomers or NBR rubbers. They have excellent oil resistance and are widely used for flexible couplings, hoses, washing machine parts, and gloves. Butyl rubbers are copolymers of isobutylene and 1.3% isoprene; they are valuable because of their good resistance to abrasion, low gas permeability, and high dielectric strength. Neoprene ( polychloroprene ) is particularly useful at elevated temperatures and is used for heavy-duty applications. Of course, Neoprene foam is the primary material of most diving suits. Neoprene is a common material for o-rings, and is also used as the basis of many contact cements.
Ethylene-propylene rubbers (RPDM) with their high resistance to weathering and sunlight are used for automobile parts, hoses, electrical insulation, and footwear. Urethane elastomers are called Spandex and they consist of urethane blocks and polyether or polyester blocks; the urethane blocks provide strength and heat resistance, the polyester and polyether blocks provide elasticity; they are the most versatile elastomer family because of their hardness, strength, oil resistance, and aging characteristics. They have replaced rubber in elasticized materials. Other uses range from airplane wheels to seat cushions. Other synthetics are highly oil-resistant, but their high cost limits their use. Silicone rubbers are organic derivatives of inorganic polymers, e.g., the polymer of dimethysilanediol. Very stable and flexible over a wide temperature range, they are used in wire and cable insulation. AquaSeal is a urethane cement.

History
Pre-Columbian peoples of South and Central America used rubber for balls, containers, and shoes and for waterproofing fabrics. Mentioned by Spanish and Portuguese writers in the 16th century, rubber did not attract the interest of Europeans until reports about it were made (1736-51) to the French Academy of Sciences by Charles de la Condamine and Francois Fresneau. Pioneer research in finding rubber solvents and in waterproofing fabrics was done before 1800, but rubber was used only for elastic bands and erasers, and these were made by cutting up pieces imported from Brazil. Joseph Priestley is credited with the discovery c.1770 of its use as an eraser, thus the name rubber.
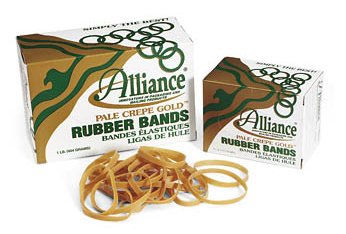
The first rubber factory in the world was established near Paris in 1803, the first in England by Thomas Hancock in 1820. Hancock devised the forerunner of the masticator ( the rollers through which the rubber is passed to partially break the polymer chains, ) and in 1835 Edwin Chaffee, an American, patented a mixing mill and a calendar ( a press for rolling the rubber into sheets. )
In 1823, Charles Macintosh found a practical process for waterproofing fabrics, and in 1839 Charles Goodyear discovered vulcanization, which revolutionized the rubber industry. On March 17, 1845, the first rubber band was patented by Stephen Perry of London. In the latter half of the 19th-century, the demand for rubber insulation by the electrical industry and the invention of the pneumatic tire extended the demand for rubber. In the 19th-century, wild rubber was harvested in South and Central America and in Africa; most of it came from the Para rubber tree of the Amazon basin.
Despite Brazil's legal restrictions, seeds of the tree were smuggled to England in 1876. The resultant seedlings were sent to Ceylon ( Sri Lanka ) and later to many tropical regions, especially the Malay area and Java and Sumatra, beginning the enormous East Asian rubber industry. Here the plantations were so carefully cultivated and managed that the relative importance of Amazon rubber diminished. American rubber companies, as a step toward diminishing foreign control of the supply, enlarged their plantation holdings in Liberia and in South and Central America.
During World War I, Germany made a synthetic rubber, but it was too expensive for peacetime use. In 1927 a less costly variety was invented, and in 1931 Neoprene was made, both in the United States. German scientists developed Buna rubber just prior to World War II. When importation of natural rubber from the East Indies was cut off during World War II, the United States began large-scale manufacture of synthetic rubber, concentrating on Buna S. Today synthetic rubber accounts for about 60% of the world's rubber production.
Edible Rubber
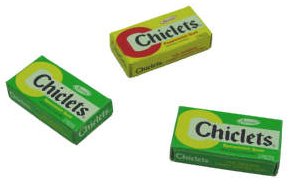
Chicle is the name for the gum obtained from the latex of the sapodilla tree ( Manilkara zapota ) a tropical American evergreen. The sapodilla ( known also by many other common names ) is widely cultivated in tropical regions, including south Florida, for its fruit, which is plum-sized with translucent yellow-brown flesh. Large-scale cultivation of the tree for latex is impractical because it can be tapped only infrequently and varies widely in yield.
Chicle is collected during the rainy season from wild trees in the rain forests. Natives, called chicleros, cut zigzag gashes in the tree trunk and collect the sap in bags. The collected material is boiled until it reaches the correct thickness and is then molded into blocks. These are exported, chiefly to the United States, for use in making chewing gum. Unsystematic and excessive tapping of the sapodilla ( especially in the Yucatan peninsula, where it was most abundant ) is leading to its depletion and has necessitated increasing use of chicle substitutes from other latex-producing plants.
Chewing gum is a confection consisting usually of chicle, flavorings, and corn syrup, and sugar or artificial sweeteners. Prehistoric people are believed to have chewed resins. Spruce resin was chewed as a thirst quencher by Native Americans, from whom pioneers adopted the custom. Refined paraffin was later used and then chicle, which was probably first imported into the United States through Mexico. A chicle gum was patented in 1869 by William and Semple.
In the present-day manufacture of chewing gum blocks of chicle are ground, melted, and cleared in a whirling vat, and then the flavorings and other ingredients are added. The gum is rolled through sheeting machinery and chopped into sticks or into candy-coated pellets. Insoluble plastics may be mixed with or substituted for the chicle. The United States is the major producer, exporter, and consumer, of chewing gum.
Plastics
A plastic is any organic material with the ability to flow into a desired shape when heat and pressure are applied to it and to retain the shape when they are withdrawn. Rubbers are really a subset of plastics, known as elastomers, although there is no clear dividing line between the two: many rubbers are quite stiff and hard, and many plastics are stretchy like rubber.
Composition and Types of Plastic
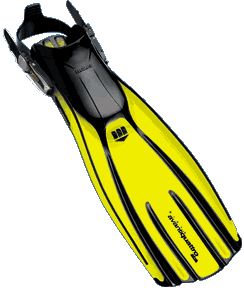
A plastic is made up principally of a binder together with plasticizers, fillers, pigments, and other additives. The binder gives a plastic its main characteristics and usually its name. Thus, polyvinyl chloride ( PVC ) is both the name of a binder and the name of a plastic into which it is made. Binders may be natural materials, e.g., cellulose derivatives, casein, or milk protein, but are more commonly synthetic resins. In either case, the binder materials consist of very long chainlike molecules called polymers.
Cellulose derivatives are made from cellulose, a naturally occurring polymer; casein is also a naturally occurring polymer. Synthetic resins are polymerized, or built up, from small simple molecules called monomers. Plasticizers are added to a binder to increase flexibility and toughness. Fillers are added to improve particular properties, e.g., hardness or resistance to shock. Pigments are used to impart various colors. Virtually any desired color or shape and many combinations of the properties of hardness, durability, elasticity, and resistance to heat, cold, and acid can be obtained in a plastic.
There are two basic types of plastic: thermosetting, which cannot be re-softened or reshaped after being subjected to heat and pressure; and thermoplastic, which can be repeatedly softened and remolded by heat and pressure. When heat and pressure are applied to a thermoplastic binder, the chainlike polymers slide past each other, giving the material "plasticity." However, when heat and pressure are initially applied to a thermosetting binder, the molecular chains become cross-linked, thus preventing any slippage if heat and pressure are reapplied.

Molding of Plastic
Plastics are available in the form of bars, tubes, sheets, coils, and blocks, and these can be fabricated to specification. However, plastic articles are commonly manufactured from plastic powders in which desired shapes are fashioned by compression, transfer, injection, or extrusion molding.
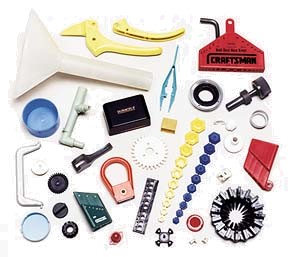
In compression molding, materials are generally placed immediately in mold cavities, where the application of heat and pressure makes them first plastic, then hard. The transfer method, in which the compound is plasticized by outside heating and then poured into a mold to harden, is used for designs with intricate shapes and great variations in wall thickness. Injection-molding machinery dissolves the plastic powder in a heating chamber and by plunger action forces it into cold molds, where the product sets.
The operations take place at rigidly controlled temperatures and intervals. Extrusion molding employs a heating cylinder, pressure, and an extrusion die through which the molten plastic is sent and from which it exits in a continuous form to be cut in lengths or coiled.
Environmental Considerations
Plastics are so durable that they will not rot or decay as do natural products such as those made of wood. As a result, great amounts of discarded plastic products accumulate in the environment as waste. It has been suggested that plastics could be made to decompose slowly when exposed to sunlight by adding certain chemicals to them. Plastics present the additional problem of being difficult to burn. When placed in an incinerator, they tend to melt quickly and flow downward, clogging the incinerator's grate. They also emit harmful fumes; e.g., burning polyvinyl chloride gives off hydrogen chloride gas.